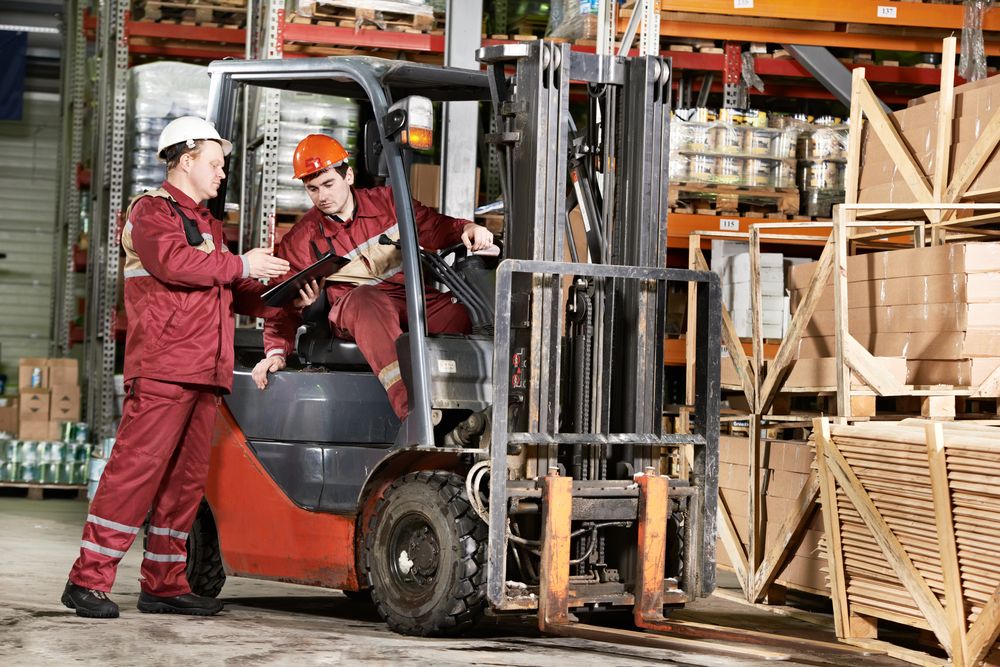
Complexity and variability are facts of life for manufacturers. Think of all the different types of goods that are manufactured around the world, from food to computers to cars—each of which have unique challenges based on their respective industry. However, what remains true across any industry is the alarming rate of expansion into the global marketplace. As a result, the industry has grown more quickly than the market for goods, creating fierce competition for business. Revenue growth has slowed as manufacturers compete for a shrinking market share. The manufacturing industry faces numerous challenges, with top line (revenue) being one of the most important concerns in today’s dynamic marketplace.
Don’t Sacrifice Quality for Efficiency
Two major factors have shaped the growing competition within the manufacturing industry. First, is the technology revolution, which has increased productivity and quality, and reduced costs worldwide. Master data management (MDM) integrates systems from all aspects of manufacturing, transforming the way companies produce and move inventory, while maintaining excellent relationships with their customers. Second, is the significant reduction in barriers to trade, particularly with respect to manufactured goods.
Manufacturers maintain precise standards and a highly controlled, automated manufacturing environment. Parts of these standards dictate clean-room productivity, while preserving rigorous quality control. Unique customer requirements need real-time event management to monitor a highly technical manufacturing process, as well as produce an appropriate response when certain critical situations occur.
Integrating Transparency into Manufacturing
Innovation is driving new manufacturing methods, materials, and processes. The complexity of this innovation is driven by engagement with a broad range of stakeholders, as well as an evolving marketplace. Internal data must be carefully managed and organized to provide necessary transparency. Integrating internal systems allows for visibility, as well as the resources to drill down to certain regions, products, or customers to solve problems or increase efficiencies.
In this environment, manufacturers need a real-time view across the value chain to better monitor and control the process in order to ensure the right products are delivered to the right customers at the right time.
Today’s supply chains are extremely complex and often span many countries and continents, which makes end-to-end synchronization a goal that continues to elude many enterprises. To combat the challenge of facilitating actionable data on time, the entire supply chain needs to be synchronized at the level of data. TIBCO helps organizations synchronize supply chains and have real-time access to data through easier integration and expansion.
From aerospace to semiconductors to diapers, TIBCO assists manufacturers in virtually every industry to stay agile by enabling real-time visibility across their business to anticipate demand, reduce supply chain risks, and route intelligence to optimize manufacturing activities.
Following the integration of their backend systems, applications, and partners, manufacturers achieve high uptime while efficiently managing their hundreds, or thousands, of global suppliers and partners—even during peak season. Integrated systems allow these organizations to synchronize production with retail partners as they identify and understand sales patterns, which allows optimization of inventory levels. While many challenges plague manufactures each year from supply and demand to material shortages and logistical issues, internal systems shouldn’t create concerns. With a clear integration strategy, manufacturers can focus on what is truly important: manufacturing processes, customers, and products.
Master Data Management is a critical piece to the systems that are propelling manufacturing to new heights. Explore why TIBCO is positioned as a leader in the Gartner MQ for Master Data Management for Customer and Product data management.