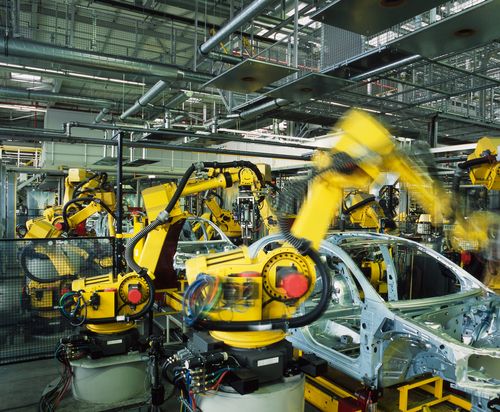
Manufacturing drives the Japanese economy and its exports are known around the world. Japan’s factories produce a remarkable share of the world’s automobiles, consumer electronics, and a host of other high-quality products. A great deal of their competitive edge comes from the use of technology, like robotics to increase the efficiency of production lines, and they remain the showcase for industry best practices for quality control. Companies from all over send their people to Japan to learn better manufacturing techniques.
Despite their leads in efficiency and quality, Japanese manufacturing is not immune to the struggles associated with managing the increasing amount of critical data. Just like many other industries, manufacturing is going through a data crisis of its own.
Current Data Management Drawbacks
As automation has increased across manufacturing, so have the number and types of software packages that run the factory. Each point solution, whether an ERP, MRP, CRM or other system, was integrated over the years with ETL tools to resolve the issue of overlapping data sets. Using ETL tools as a solution was a quick way to extract, transform, and load data into central data warehouses, but it fails to serve business needs on several fronts:
- Information isn’t updated in real time, leading to a constant lag in information between batch processes
- Inconsistent data requires complex, fragile rules to determine which data to use
- The speed of ETL tools built upon traditional databases is too slow to be used for operational decisions
- Integrating new data sources is slow and requires extensive testing cycles
Systems Don’t talk to Systems
As organizations expand and acquire more products and manufacturing locations, so does the data load. This increases the importance of a centralized data management tool and increases the problems that ETL introduces. For example, let’s say a Japan-based corporation acquires a manufacturing location and a new product in Germany. This new product uses some of the same materials that are presently procured for the manufacturing location in Japan. However, if the two systems are not able to communicate that each location is using the same materials, and perhaps the same vendors, manufacturers may be missing out on a significant cost-saving opportunity. When systems are able to efficiently communicate this information, it can mean big savings for an organization. It allows them to negotiate the best prices and services from vendors because they now represent a larger customer with greater buying power.
Operations abroad will continue to expand, which will only further increase the need for centralized data management. Efficient centralized data management will become a measure of manufacturing quality. Manufacturers all over the world have their eyes on best practices in Japan; it becomes more critical that the data challenges are addressed in the correct manner. This means not only considering legacy applications, but looking to the future in anticipation of new data management capabilities as a criteria for a sound integration strategy. Success in Japan with well-managed data across many operations means success for manufacturing as an industry.
Curious about where your company stands in system integration? Take the Integration Maturity Assessment.